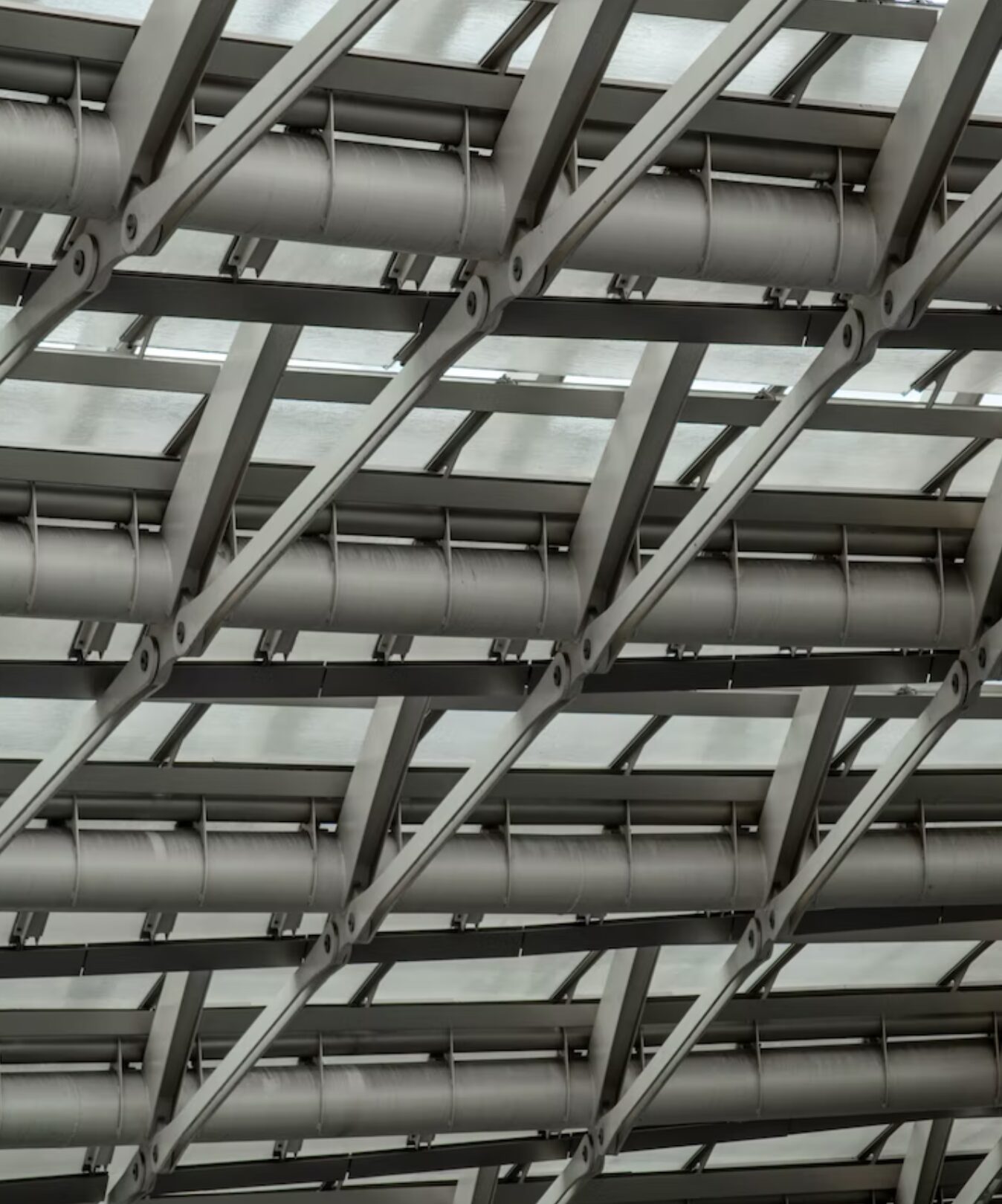
Steel plate rolling involves passing a piece of steel plate through one or more pairs of rollers in order to reduce the overall thickness of the material. This process also ensures that the workpiece thickness is unchanging throughout. Hot rolling and cold rolling are two different processes used in steel plate rolling.
Hot rolling involves heating the steel plate above its recrystallization temperature, which is typically around 1700°F (925°C) for steel. This makes the steel plate more malleable and easier to shape. Hot rolling is commonly used for producing thick steel plates, and it can also improve the mechanical properties of the material.
Cold rolling, on the other hand, involves rolling the steel plate at room temperature or below its recrystallization temperature. This makes the steel plate harder and stronger, but also more brittle. Cold rolling is commonly used for producing thin steel plates, and it can also improve the surface finish and dimensional accuracy of the material.
Types of rolling processes
There are many different types of rolling processes, including:
- Ring rolling: This process involves shaping a metal ring by gradually reducing its thickness and increasing its diameter by rolling it between two rollers. It is commonly used in the manufacturing of bearings, gears, and other circular components.
- Roll forming: In this process, a continuous metal sheet is fed through a series of rollers that gradually bend it into the desired shape. It is commonly used in the production of long, uniform shapes such as metal roofing or steel studs.
- Roll bending: This process involves bending a metal plate or sheet into a curved shape by passing it between three rollers, each of which applies pressure at a different point on the material. It is commonly used in the manufacturing of pipes, tubes, and other curved components.
- Profile rolling: This process involves shaping a metal bar or rod into a specific profile by gradually reducing its thickness and increasing its width or height. It is commonly used in the manufacturing of structural components such as rails, beams, and channels.
- Controlled rolling:This process involves heating a metal plate to a specific temperature and then rolling it to achieve a specific grain structure and mechanical properties. It is commonly used in the manufacturing of high-strength steel plates for structural applications.
More information
-
Hot Rolling
Hot rolling processes more weight than any other manufacturing process available. Finished products are usually of a very high quality but can be left covered in mill scale due to the high-temperatures during processing. This oxide is removed via pickling to leave behind a smooth surface. This method is usually employed to produce sheet metal or other materials, including:
• Automotive parts (frames, wheels, water heaters etc.)
• Agricultural equipment
• Compressor shells
• Metal buildings
• Guard rails -
Cold Rolling
Cold rolling increases a material’s strength, improves the surface finish and maintains tighter tolerances. However, cold rolling cannot reduce the thickness of a material as well as hot rolling can, especially in a single pass. Cold rolled sheets and strips come in various conditions:
• Full-hard
• Half-hard
• Quarter-hard
• Skin-rolled -
Full-hard cold rolling
Full-hard cold rolling reduces a material’s thickness by up to 50%. Each respective condition then reduces less thickness as we go down the list, finishing with skin-rolling that reduces thickness by no more than 1%. This last condition is used more commonly to provide a uniform finish. Common applications of cold rolling include smaller parts such as:
• Metal furniture
• Motorcycle parts
• Lighting fixtures
• Hinges